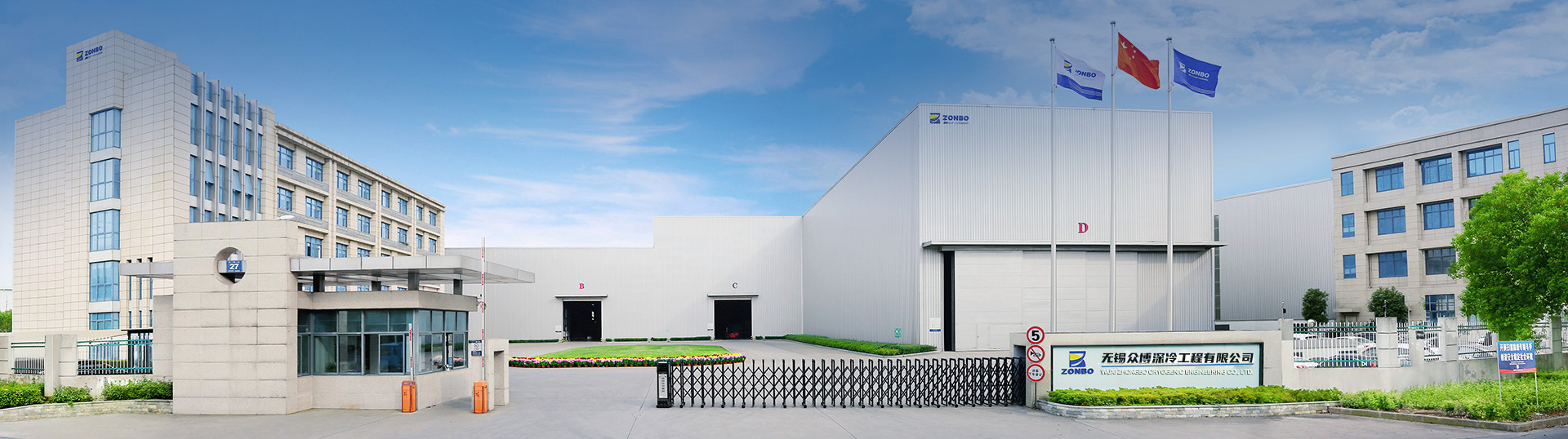
NEWS
What are the performance advantages of aluminum plate-fin heat exchangers?
The performance advantages of aluminum plate-fin heat exchangers are obvious, mainly reflected in the following aspects:
1. High heat transfer efficiency
Structural enhanced heat transfer: The special structure of the fins creates strong turbulence in the fluid, causing the thermal boundary layer to continuously rupture and renew, significantly reducing thermal resistance and improving heat transfer efficiency. Its heat transfer coefficient is 5-10 times higher than that of a shell and tube heat exchanger, and the total heat transfer coefficient can reach 500-3000W/(m ² · K).
Large heat transfer area per unit volume: The heat transfer area per unit volume is generally 1500-2500m ²/m ³, which is 8-20 times that of a shell and tube heat exchanger, greatly improving the heat transfer capacity per unit volume.
2. Compact structure and light weight
Small size and light weight: With a compact structure, the weight is only one tenth of that of a shell and tube heat exchanger with the same heat transfer area. The metal consumption per unit heat transfer area can be several tens of times smaller than that of a shell and tube heat exchanger, saving space and material costs.
Extended secondary heat transfer surface: The fins form an extended secondary heat transfer surface, and the heat transfer process not only occurs on the primary heat transfer surface (partition), but also simultaneously on the secondary heat transfer surface (fins), improving heat transfer efficiency.
3. Wide adaptability range
Multi medium heat transfer: It can be applied to heat transfer between various media such as gas gas, gas-liquid, and liquid-liquid, meeting the needs of different working conditions.
Multi stream heat exchange: Up to 13 streams can be exchanged simultaneously in the same plate-fin heat exchanger, and heat can be extracted from different temperature points according to process requirements, with high flexibility.
Wide temperature range: Suitable for temperatures ranging from -270 ℃ to+200 ℃, it can meet the requirements of working conditions from ultra-low temperature to high temperature.
Strong pressure bearing capacity: The fins and baffles are tightly connected by brazing technology, with high pressure bearing capacity. Some large plate-fin heat exchangers can withstand pressure up to 8MPa.
4. High reliability
Fully brazed structure: eliminates the possibility of leakage, while the fins serve as both heat transfer surfaces and supports, with high strength, ensuring long-term stable operation of the equipment.
Good sealing: The brazing process ensures a tight connection between the fins and the partition, with low leakage rate, improving the reliability and safety of the equipment.
5. Good flexibility and economy
Flexible arrangement of flow channels: The arrangement and combination of flow channels can adapt to different working conditions such as counterflow, cross flow, multi stream flow, and multi process heat transfer, meeting complex process requirements.
Low cost: Due to its compact structure, light weight, and the ability to be made of aluminum alloy, the cost is low and the economy is good.
6. Good temperature control
Accurate temperature control: The unique structure of the fins ensures uniform distribution of fluid in the flow channel, stable temperature field, and facilitates accurate temperature control.
1. High heat transfer efficiency
Structural enhanced heat transfer: The special structure of the fins creates strong turbulence in the fluid, causing the thermal boundary layer to continuously rupture and renew, significantly reducing thermal resistance and improving heat transfer efficiency. Its heat transfer coefficient is 5-10 times higher than that of a shell and tube heat exchanger, and the total heat transfer coefficient can reach 500-3000W/(m ² · K).
Large heat transfer area per unit volume: The heat transfer area per unit volume is generally 1500-2500m ²/m ³, which is 8-20 times that of a shell and tube heat exchanger, greatly improving the heat transfer capacity per unit volume.
2. Compact structure and light weight
Small size and light weight: With a compact structure, the weight is only one tenth of that of a shell and tube heat exchanger with the same heat transfer area. The metal consumption per unit heat transfer area can be several tens of times smaller than that of a shell and tube heat exchanger, saving space and material costs.
Extended secondary heat transfer surface: The fins form an extended secondary heat transfer surface, and the heat transfer process not only occurs on the primary heat transfer surface (partition), but also simultaneously on the secondary heat transfer surface (fins), improving heat transfer efficiency.
3. Wide adaptability range
Multi medium heat transfer: It can be applied to heat transfer between various media such as gas gas, gas-liquid, and liquid-liquid, meeting the needs of different working conditions.
Multi stream heat exchange: Up to 13 streams can be exchanged simultaneously in the same plate-fin heat exchanger, and heat can be extracted from different temperature points according to process requirements, with high flexibility.
Wide temperature range: Suitable for temperatures ranging from -270 ℃ to+200 ℃, it can meet the requirements of working conditions from ultra-low temperature to high temperature.
Strong pressure bearing capacity: The fins and baffles are tightly connected by brazing technology, with high pressure bearing capacity. Some large plate-fin heat exchangers can withstand pressure up to 8MPa.
4. High reliability
Fully brazed structure: eliminates the possibility of leakage, while the fins serve as both heat transfer surfaces and supports, with high strength, ensuring long-term stable operation of the equipment.
Good sealing: The brazing process ensures a tight connection between the fins and the partition, with low leakage rate, improving the reliability and safety of the equipment.
5. Good flexibility and economy
Flexible arrangement of flow channels: The arrangement and combination of flow channels can adapt to different working conditions such as counterflow, cross flow, multi stream flow, and multi process heat transfer, meeting complex process requirements.
Low cost: Due to its compact structure, light weight, and the ability to be made of aluminum alloy, the cost is low and the economy is good.
6. Good temperature control
Accurate temperature control: The unique structure of the fins ensures uniform distribution of fluid in the flow channel, stable temperature field, and facilitates accurate temperature control.