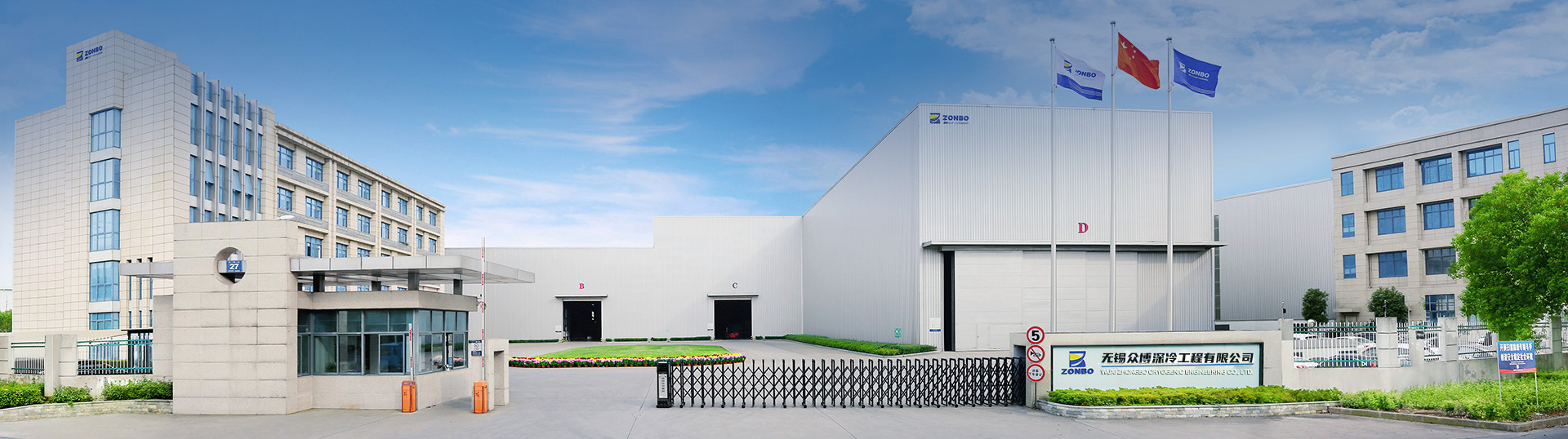
NEWS
Technical characteristics of coil-wound heat exchanger
The technical characteristics of coil-wound heat exchangers are mainly reflected in the following aspects:
Compact structure, large heat transfer area:
The coil heat exchanger adopts a spiral winding structure, which provides a large heat transfer area per unit volume. For example, for heat transfer tubes with a diameter of 8-12 millimeters, the heat transfer area per cubic meter can reach 100-170 square meters, which is much higher than that of ordinary shell and tube heat exchangers.
High heat exchange efficiency:
The special structural design of the coil-wound heat exchanger creates strong turbulence in the shell side fluid, while the strengthening effect of the helical flow inside the tube also increases the heat transfer film coefficient of the tube side. Under certain specific conditions, the total heat transfer coefficient of the coil-wound heat exchanger can reach over 500W/(m ² · K), significantly improving the heat transfer efficiency.
Simultaneous heat transfer through multiple media:
The coil-wound heat exchanger can meet the simultaneous heat transfer of multiple fluids in one device by setting up multiple tube passes (single shell pass). This feature greatly improves heat transfer efficiency and applicability, especially suitable for industrial applications that require simultaneous processing of multiple media.
High voltage resistance:
The diameter of the heat exchange tubes on the tube side of the coil heat exchanger is small and can withstand high pressure. The operating pressure can reach 22MPa or even higher, which gives the coil-wound heat exchanger a significant advantage under high-pressure conditions.
Good thermal expansion compensation:
The heat exchange tube end of the coil-wound heat exchanger has a certain length of free bending section, which has good flexibility. This design allows the thermal expansion of the heat transfer tube to partially compensate for itself, reducing the stress impact on the tube plate welding and minimizing the possibility of leakage at the tube head and tube plate welds.
Strong anti scaling ability:
The spiral winding structure of the tube heat exchanger generates secondary circulation when the fluid flows inside the tube, which helps to reduce fouling deposition. At the same time, the turbulence formed by the shell side fluid between each pipe layer also reduces the probability of fluid adhesion to the wall, thereby reducing the tendency for scaling.
Stable and reliable operation:
The resonance problem was fully considered in the structural design of the coil-wound heat exchanger, effectively suppressing the phenomenon of acoustic standing wave vibration. This makes the operation of the coil heat exchanger stable and reliable, with low noise.
Large scale and customization potential:
The coil-wound heat exchanger supports large-scale design and can increase heat transfer capacity by increasing the size and number of coil-wound bundles. At the same time, its modular structure can meet the customized requirements of different processes for heat transfer area, medium type, and operating pressure.
Compact structure, large heat transfer area:
The coil heat exchanger adopts a spiral winding structure, which provides a large heat transfer area per unit volume. For example, for heat transfer tubes with a diameter of 8-12 millimeters, the heat transfer area per cubic meter can reach 100-170 square meters, which is much higher than that of ordinary shell and tube heat exchangers.
High heat exchange efficiency:
The special structural design of the coil-wound heat exchanger creates strong turbulence in the shell side fluid, while the strengthening effect of the helical flow inside the tube also increases the heat transfer film coefficient of the tube side. Under certain specific conditions, the total heat transfer coefficient of the coil-wound heat exchanger can reach over 500W/(m ² · K), significantly improving the heat transfer efficiency.
Simultaneous heat transfer through multiple media:
The coil-wound heat exchanger can meet the simultaneous heat transfer of multiple fluids in one device by setting up multiple tube passes (single shell pass). This feature greatly improves heat transfer efficiency and applicability, especially suitable for industrial applications that require simultaneous processing of multiple media.
High voltage resistance:
The diameter of the heat exchange tubes on the tube side of the coil heat exchanger is small and can withstand high pressure. The operating pressure can reach 22MPa or even higher, which gives the coil-wound heat exchanger a significant advantage under high-pressure conditions.
Good thermal expansion compensation:
The heat exchange tube end of the coil-wound heat exchanger has a certain length of free bending section, which has good flexibility. This design allows the thermal expansion of the heat transfer tube to partially compensate for itself, reducing the stress impact on the tube plate welding and minimizing the possibility of leakage at the tube head and tube plate welds.
Strong anti scaling ability:
The spiral winding structure of the tube heat exchanger generates secondary circulation when the fluid flows inside the tube, which helps to reduce fouling deposition. At the same time, the turbulence formed by the shell side fluid between each pipe layer also reduces the probability of fluid adhesion to the wall, thereby reducing the tendency for scaling.
Stable and reliable operation:
The resonance problem was fully considered in the structural design of the coil-wound heat exchanger, effectively suppressing the phenomenon of acoustic standing wave vibration. This makes the operation of the coil heat exchanger stable and reliable, with low noise.
Large scale and customization potential:
The coil-wound heat exchanger supports large-scale design and can increase heat transfer capacity by increasing the size and number of coil-wound bundles. At the same time, its modular structure can meet the customized requirements of different processes for heat transfer area, medium type, and operating pressure.