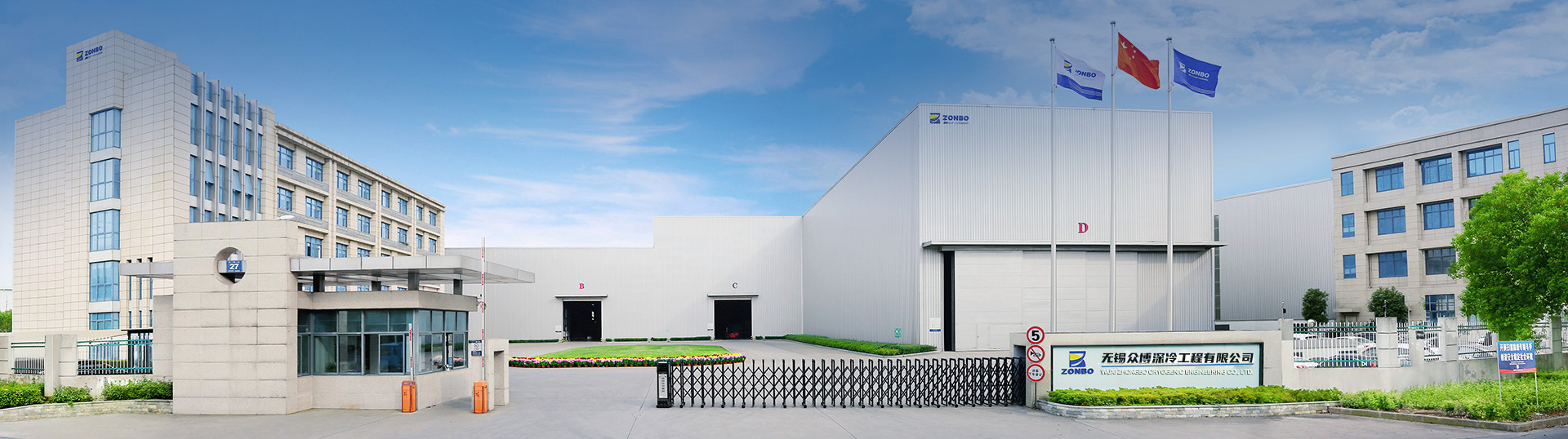
NEWS
What is the heat transfer efficiency of aluminum plate-fin heat exchangers?
The heat transfer efficiency of aluminum plate-fin heat exchangers is significantly higher than that of traditional heat exchangers, and its core advantages are reflected in the following key performance indicators:
Advantage of heat transfer area per unit volume
The unit volume heat transfer area of this device can reach 1500-2500m ²/m ³, which is 8-20 times that of shell and tube heat exchangers. Through a compact stacked flow channel design, more heat exchange units can be arranged in the same volume, achieving higher efficiency in heat transfer.
Enhanced convective heat transfer coefficient
Fin structure enhances heat transfer performance through forced turbulence mechanism:
Sawtooth fins can cause periodic rupture of the fluid boundary layer, and the heat release coefficient is increased by more than 30% compared to flat fins;
Ripple fins enhance disturbance through sudden changes in fluid flow direction, and thermal resistance boundary layer micro rupture increases heat transfer efficiency by 15% -25%;
Porous fins continuously fracture the thermal resistance boundary layer through their porous structure, enhancing heat transfer while optimizing fluid distribution.
Overall heat transfer coefficient improvement
Its total heat transfer coefficient reaches 500-3000W/(m ² · K), which is 5-10 times that of a shell and tube heat exchanger. This advantage stems from:
Expansion effect of secondary heat transfer surface on fins;
High thermal conductivity of partitions and fins (aluminum thermal conductivity of 203.5W/(m · K));
Enhanced convective heat transfer due to increased turbulence intensity within the flow channel.
Multi stream collaborative heat transfer effect
The device supports synchronous heat transfer of 13 fluids, and through a counter current cross flow combination channel design, the average logarithmic temperature difference correction coefficient reaches 0.95. The synergistic effect of multiple streams can achieve:
Cascade utilization of heat under complex operating conditions;
Matching of heat extraction requirements at different temperature points;
Uniformization of temperature field within the heat exchange unit.
Thermal boundary layer control technology
The geometric parameters of the fins (height 2-10mm, thickness 0.1-0.3mm, spacing 1-5mm) have been optimized to control the thickness of the thermal boundary layer within the range of 0.1-0.5mm. By continuously disrupting the stability of the boundary layer and maintaining high turbulence of the fluid (Re number>10 ?), the thermal resistance is significantly reduced.
Advantage of heat transfer area per unit volume
The unit volume heat transfer area of this device can reach 1500-2500m ²/m ³, which is 8-20 times that of shell and tube heat exchangers. Through a compact stacked flow channel design, more heat exchange units can be arranged in the same volume, achieving higher efficiency in heat transfer.
Enhanced convective heat transfer coefficient
Fin structure enhances heat transfer performance through forced turbulence mechanism:
Sawtooth fins can cause periodic rupture of the fluid boundary layer, and the heat release coefficient is increased by more than 30% compared to flat fins;
Ripple fins enhance disturbance through sudden changes in fluid flow direction, and thermal resistance boundary layer micro rupture increases heat transfer efficiency by 15% -25%;
Porous fins continuously fracture the thermal resistance boundary layer through their porous structure, enhancing heat transfer while optimizing fluid distribution.
Overall heat transfer coefficient improvement
Its total heat transfer coefficient reaches 500-3000W/(m ² · K), which is 5-10 times that of a shell and tube heat exchanger. This advantage stems from:
Expansion effect of secondary heat transfer surface on fins;
High thermal conductivity of partitions and fins (aluminum thermal conductivity of 203.5W/(m · K));
Enhanced convective heat transfer due to increased turbulence intensity within the flow channel.
Multi stream collaborative heat transfer effect
The device supports synchronous heat transfer of 13 fluids, and through a counter current cross flow combination channel design, the average logarithmic temperature difference correction coefficient reaches 0.95. The synergistic effect of multiple streams can achieve:
Cascade utilization of heat under complex operating conditions;
Matching of heat extraction requirements at different temperature points;
Uniformization of temperature field within the heat exchange unit.
Thermal boundary layer control technology
The geometric parameters of the fins (height 2-10mm, thickness 0.1-0.3mm, spacing 1-5mm) have been optimized to control the thickness of the thermal boundary layer within the range of 0.1-0.5mm. By continuously disrupting the stability of the boundary layer and maintaining high turbulence of the fluid (Re number>10 ?), the thermal resistance is significantly reduced.