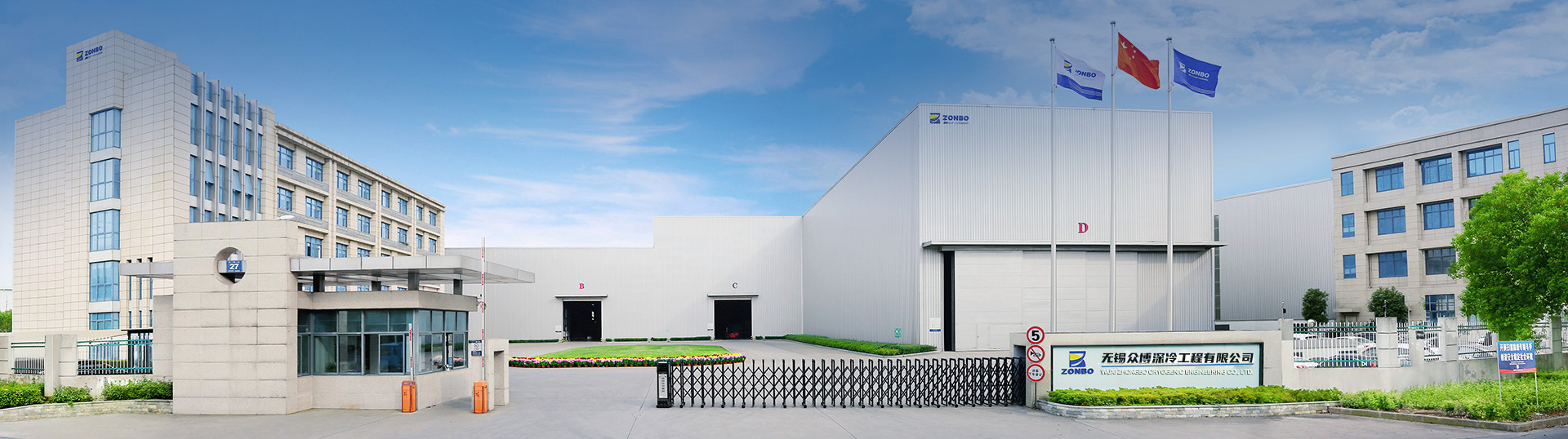
NEWS
Key points for manufacturing and inspection of aluminum pressure vessels
The manufacturing and inspection of aluminum pressure vessels require strict control over key aspects such as material characteristics, welding processes, structural design, and inspection methods to ensure their safety and reliability. The following is a detailed analysis of the key points:
1、 Manufacturing key points
Material selection and preparation
Alloy selection: Choose high-strength and corrosion-resistant aluminum alloys based on the usage scenario, such as 5083, 5454, etc. Design pressure (not exceeding 1.6MPa) and temperature (not exceeding 150 ℃) should be considered to avoid a decrease in strength at high temperatures.
Material acceptance: Check the quality certificate and transfer of material markings to ensure that the materials meet the standards. For critical components, retesting and non-destructive testing are required.
Surface treatment: prevent direct contact between aluminum and steel to avoid electrochemical corrosion; Isolation measures should be taken for containers containing liquid media.
Structure design
Avoid high-speed fluid erosion: Aluminum containers have poor erosion resistance and need to limit the flow rate of the medium (corrosive medium flow rate<1.5m/s, clear water flow rate needs to be lower).
Reduce stress concentration: Optimize the opening reinforcement structure, avoid sharp corners and abrupt changes, and prevent stress corrosion cracking.
Connection method: Steel sleeve flanges are preferred for connecting flanges; Threaded connections require anti bite measures and use high-strength aluminum or steel bolts.
procedure
Welding method: MIG welding or TIG welding should be used to avoid gas welding and aluminum coated electrode welding. Before welding, it is necessary to thoroughly remove impurities such as oxide film and oil stains.
Process evaluation: Conduct welding process evaluation to ensure the quality of the weld seam. During the welding process, it is necessary to control the heat input to prevent overheating from causing coarse grains.
Post weld treatment: Generally, heat treatment is not required, but the density and mechanical properties of the weld seam need to be checked to prevent shrinkage, porosity, and hot cracking.
Forming and processing
Connection between the head and the cylinder: using structures such as flanged sleeve flanges and high neck sleeve flanges to ensure connection strength and sealing.
Flat cover and simplified connection: Choose the appropriate connection method according to the pressure level to ensure the rigidity and sealing of the flat cover.
Connection between takeover and flange: Choose the appropriate connection structure based on wall thickness and pressure to avoid stress concentration.
2、 Key inspection points
Appearance and geometric dimension inspection
Macroscopic inspection: Check the outer surface of the container for defects such as cracks, deformations, leaks, and local overheating; Check if the accessories are complete, flexible, and reliable; Check if the anchor bolts are damaged.
Dimensional measurement: check the misalignment and angle of the longitudinal and circumferential welds; Check the excess height of the weld seam and the thickness of the fillet weld seam; Check the surface roughness and straight edge height of the head.
NDT
Ultrasonic testing (UT): used to detect internal defects in welds, such as cracks, lack of fusion, etc.
Radiographic Testing (RT): Suitable for the inspection of butt joints, it can detect defects such as internal pores and slag inclusions.
Penetration testing (PT): used to detect surface opening defects such as cracks, pores, etc. Due to the non-magnetic nature of aluminum, magnetic particle testing (MT) cannot be used.
Voltage withstand test and leakage test
Pressure test: Conduct a hydrostatic or pneumatic test with a test pressure of 1.25-1.5 times the design pressure to verify the strength and sealing of the container.
Leakage test: For containers with toxic media or production processes that do not allow leakage, an air tightness test must be conducted to ensure no leakage.
Physical and chemical testing and metallographic analysis
Material inspection: Identify the type and grade of the main pressure bearing component material, and check whether the material has deteriorated.
Metallographic examination: For containers that may cause changes in the metallographic structure of metal materials, metallographic analysis is performed to check grain size, inclusions, etc.
Safety Attachment Inspection
Inspection content: Confirm the quantity, specifications, models, and product certificates of safety accessories (such as safety valves, pressure gauges, level gauges, etc.) to ensure that they meet the requirements of the design documents.
Regular inspection and maintenance
External inspection: At least once a year, inspect the container body, interface parts, welding joints, etc. for any abnormalities.
Internal and external inspection: According to the safety status level, it should be conducted every 3-6 years, including macroscopic inspection, wall thickness measurement, non-destructive testing, etc.
Maintenance: Regularly inspect the anti-corrosion layer and insulation layer, promptly address corrosion, wear and tear issues, and ensure the long-term safe operation of the container.
1、 Manufacturing key points
Material selection and preparation
Alloy selection: Choose high-strength and corrosion-resistant aluminum alloys based on the usage scenario, such as 5083, 5454, etc. Design pressure (not exceeding 1.6MPa) and temperature (not exceeding 150 ℃) should be considered to avoid a decrease in strength at high temperatures.
Material acceptance: Check the quality certificate and transfer of material markings to ensure that the materials meet the standards. For critical components, retesting and non-destructive testing are required.
Surface treatment: prevent direct contact between aluminum and steel to avoid electrochemical corrosion; Isolation measures should be taken for containers containing liquid media.
Structure design
Avoid high-speed fluid erosion: Aluminum containers have poor erosion resistance and need to limit the flow rate of the medium (corrosive medium flow rate<1.5m/s, clear water flow rate needs to be lower).
Reduce stress concentration: Optimize the opening reinforcement structure, avoid sharp corners and abrupt changes, and prevent stress corrosion cracking.
Connection method: Steel sleeve flanges are preferred for connecting flanges; Threaded connections require anti bite measures and use high-strength aluminum or steel bolts.
procedure
Welding method: MIG welding or TIG welding should be used to avoid gas welding and aluminum coated electrode welding. Before welding, it is necessary to thoroughly remove impurities such as oxide film and oil stains.
Process evaluation: Conduct welding process evaluation to ensure the quality of the weld seam. During the welding process, it is necessary to control the heat input to prevent overheating from causing coarse grains.
Post weld treatment: Generally, heat treatment is not required, but the density and mechanical properties of the weld seam need to be checked to prevent shrinkage, porosity, and hot cracking.
Forming and processing
Connection between the head and the cylinder: using structures such as flanged sleeve flanges and high neck sleeve flanges to ensure connection strength and sealing.
Flat cover and simplified connection: Choose the appropriate connection method according to the pressure level to ensure the rigidity and sealing of the flat cover.
Connection between takeover and flange: Choose the appropriate connection structure based on wall thickness and pressure to avoid stress concentration.
2、 Key inspection points
Appearance and geometric dimension inspection
Macroscopic inspection: Check the outer surface of the container for defects such as cracks, deformations, leaks, and local overheating; Check if the accessories are complete, flexible, and reliable; Check if the anchor bolts are damaged.
Dimensional measurement: check the misalignment and angle of the longitudinal and circumferential welds; Check the excess height of the weld seam and the thickness of the fillet weld seam; Check the surface roughness and straight edge height of the head.
NDT
Ultrasonic testing (UT): used to detect internal defects in welds, such as cracks, lack of fusion, etc.
Radiographic Testing (RT): Suitable for the inspection of butt joints, it can detect defects such as internal pores and slag inclusions.
Penetration testing (PT): used to detect surface opening defects such as cracks, pores, etc. Due to the non-magnetic nature of aluminum, magnetic particle testing (MT) cannot be used.
Voltage withstand test and leakage test
Pressure test: Conduct a hydrostatic or pneumatic test with a test pressure of 1.25-1.5 times the design pressure to verify the strength and sealing of the container.
Leakage test: For containers with toxic media or production processes that do not allow leakage, an air tightness test must be conducted to ensure no leakage.
Physical and chemical testing and metallographic analysis
Material inspection: Identify the type and grade of the main pressure bearing component material, and check whether the material has deteriorated.
Metallographic examination: For containers that may cause changes in the metallographic structure of metal materials, metallographic analysis is performed to check grain size, inclusions, etc.
Safety Attachment Inspection
Inspection content: Confirm the quantity, specifications, models, and product certificates of safety accessories (such as safety valves, pressure gauges, level gauges, etc.) to ensure that they meet the requirements of the design documents.
Regular inspection and maintenance
External inspection: At least once a year, inspect the container body, interface parts, welding joints, etc. for any abnormalities.
Internal and external inspection: According to the safety status level, it should be conducted every 3-6 years, including macroscopic inspection, wall thickness measurement, non-destructive testing, etc.
Maintenance: Regularly inspect the anti-corrosion layer and insulation layer, promptly address corrosion, wear and tear issues, and ensure the long-term safe operation of the container.