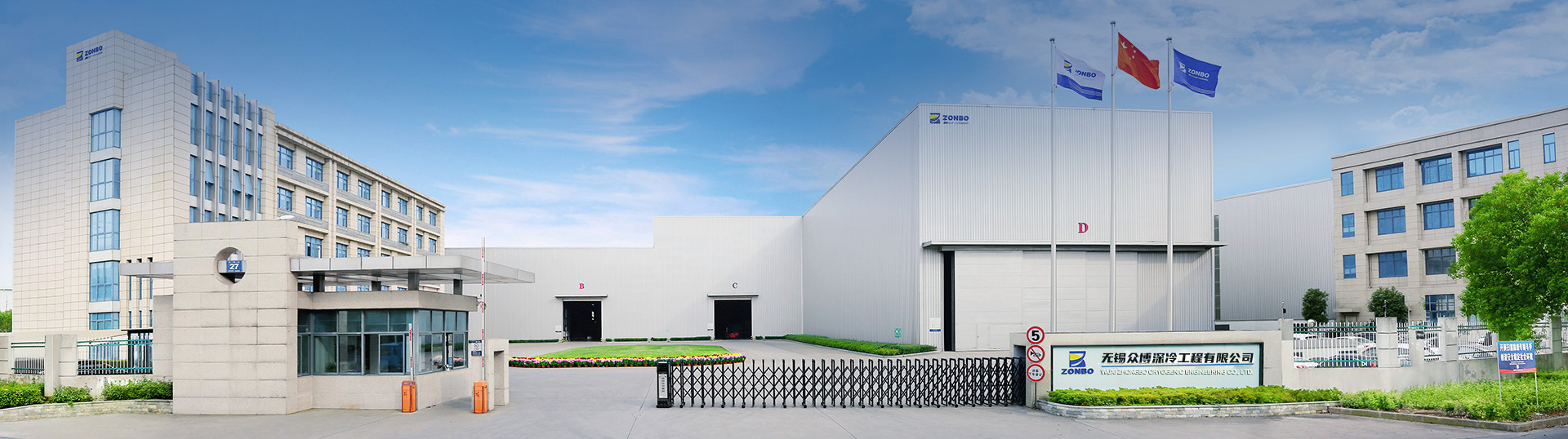
NEWS
What are the core structural components of a shell and tube heat exchanger?
The core structural composition of a shell and tube heat exchanger is the basis for its heat exchange function. The following is a structured analysis based on industrial design logic from three dimensions: the main frame, fluid separation and guiding components, and sealing and support system:
1、 Main framework: synergistic effect of shell and tube bundle
Shell (main body of pressure vessel)
Function: As an external load-bearing space for heat exchange media, it can withstand shell side fluid pressure (usually 0.1-10 MPa) and provide a heat exchange site.
Design points:
Material selection: Choose carbon steel (conventional working conditions), stainless steel (chlorine containing medium), or titanium (strong corrosive environment) based on the corrosiveness of the medium.
Strength design: Optimize wall thickness through finite element analysis to ensure no deformation occurs under high temperature and high pressure (such as 400 ℃, 8MPa).
Maintenance interface: Install manholes or handholes (diameter ≥ 400mm) for internal inspection and cleaning.
Bundle (core heat exchange unit)
Heat exchange tube:
Specification: Outer diameter 12-25mm, wall thickness 1.5-3mm, length 3-6m, commonly used material is 304/316L stainless steel.
Arrangement method: equilateral triangle arrangement (high heat transfer efficiency) or square arrangement (easy to clean), with a pipe spacing of 1.25-1.5 times the pipe diameter.
Enhanced heat transfer: using threaded tubes (with a 20% increase in heat transfer coefficient), corrugated tubes (with enhanced turbulence), or inserted turbulence elements (such as spiral ties).
Tube plate:
Structure: A circular steel plate with a thickness of 20-100mm, with a hole in the center area to fix the heat exchange tube, and the edge welded to the shell.
Connection process: Combining strength welding (high pressure resistance) with adhesive expansion (leakage prevention), the weld seam is ensured to have zero defects through penetration testing (PT).
2、 Fluid separation and guiding components: achieving countercurrent heat transfer
Head (fluid distributor)
Type:
Fixed tube plate: Welding the head and tube plate, suitable for working conditions with a temperature difference of ≤ 50 ℃.
Floating head type: One end of the head can float, suitable for situations with a temperature difference of 100-150 ℃ (such as steam condensation).
U-shaped tube type: The heat exchange tube is bent into a U-shape, allowing for axial thermal expansion and suitable for extreme working conditions with a temperature difference greater than 150 ℃.
Flow diversion design: Flow deflectors (such as bow shaped baffles) are installed inside the head to evenly distribute the fluid to each heat exchange tube and avoid flow deviation.
Baffle plate (shell side fluid reinforcement component)
Function:
Change the flow direction of the shell side fluid to form multiple turbulent flows across the tube bundle (Reynolds number Re>10 ?).
Support the tube bundle to prevent vibration (anti vibration bars need to be added when the critical flow velocity is less than 3m/s).
Type and Parameters:
Single bow: The gap height is 20% -25% of the shell diameter, suitable for cleaning media.
Double bow: symmetrically arranged with notches, reducing pressure drop by 30%, suitable for high viscosity fluids.
Spiral baffle: continuous spiral channel, shell side heat transfer coefficient increased by 15% -20%, but manufacturing cost increased by 40%.
3、 Sealing and support system: ensuring long-term stable operation
Sealing structure
Tube side sealing: Heat exchange tubes and tube sheets are sealed by mechanical expansion (pressure ≤ 10MPa) or hydraulic expansion (pressure ≤ 30MPa).
Shell side seal:
Fixed tube plate: The shell is welded to the tube plate without dynamic sealing.
Floating head type: using packing seal (graphite packing) or mechanical seal (temperature resistant to 350 ℃), leakage rate ≤ 10 ?? Pa · m ³/s.
U-shaped tube type: The tube plate and shell are sealed with gaskets (commonly metal wrapped gaskets), with a temperature resistance range of -200 ℃ to 800 ℃.
Supporting and anti vibration components
Pull rod and distance tube:
Rod: Round steel with a diameter of 10-20mm, connecting the baffle plate and the tube plate, capable of withstanding fluid impact force (tensile strength ≥ 400MPa).
Distance tube: Length error ≤ ± 0.5mm, ensuring consistent spacing between baffles and maintaining fluid turbulence.
Anti vibration design:
Misalignment of baffle notches: Adjacent baffle notches rotate 90 °, disrupting fluid resonance frequency.
Damper: Install rubber damping blocks at the free end of the tube bundle to reduce vibration amplitude (≤ 0.1mm).
4、 Structural optimization direction (engineering application case)
Compact design:
Double shell structure: The shell is divided into two stages by longitudinal partitions, increasing the heat transfer area by 30% and suitable for large temperature difference conditions (such as atmospheric and vacuum distillation units in refineries).
Microchannel heat exchange tube: with a diameter of ≤ 3mm and a heat transfer area of 2500m ²/m ³ per unit volume, it is used for heat dissipation in electronic devices.
Anti dirt design:
Online cleaning: Install a rotating nozzle (pressure 0.5-1.0MPa) on the shell side and regularly flush the scaling layer (such as seawater desalination pretreatment).
Self cleaning coating: Nano hydrophobic coating (contact angle>150 °) is applied inside the tube, reducing dirt deposition by 60%.
Material upgrade:
High temperature resistant alloy: Inconel 625 (temperature resistance of 1000 ℃) is used instead of 304 stainless steel in gas turbine intercoolers.
Graphite heat exchange tube: corrosion-resistant and high thermal conductivity (120W/(m · K)), used in strong acid and alkali media (such as chlor alkali industry).
1、 Main framework: synergistic effect of shell and tube bundle
Shell (main body of pressure vessel)
Function: As an external load-bearing space for heat exchange media, it can withstand shell side fluid pressure (usually 0.1-10 MPa) and provide a heat exchange site.
Design points:
Material selection: Choose carbon steel (conventional working conditions), stainless steel (chlorine containing medium), or titanium (strong corrosive environment) based on the corrosiveness of the medium.
Strength design: Optimize wall thickness through finite element analysis to ensure no deformation occurs under high temperature and high pressure (such as 400 ℃, 8MPa).
Maintenance interface: Install manholes or handholes (diameter ≥ 400mm) for internal inspection and cleaning.
Bundle (core heat exchange unit)
Heat exchange tube:
Specification: Outer diameter 12-25mm, wall thickness 1.5-3mm, length 3-6m, commonly used material is 304/316L stainless steel.
Arrangement method: equilateral triangle arrangement (high heat transfer efficiency) or square arrangement (easy to clean), with a pipe spacing of 1.25-1.5 times the pipe diameter.
Enhanced heat transfer: using threaded tubes (with a 20% increase in heat transfer coefficient), corrugated tubes (with enhanced turbulence), or inserted turbulence elements (such as spiral ties).
Tube plate:
Structure: A circular steel plate with a thickness of 20-100mm, with a hole in the center area to fix the heat exchange tube, and the edge welded to the shell.
Connection process: Combining strength welding (high pressure resistance) with adhesive expansion (leakage prevention), the weld seam is ensured to have zero defects through penetration testing (PT).
2、 Fluid separation and guiding components: achieving countercurrent heat transfer
Head (fluid distributor)
Type:
Fixed tube plate: Welding the head and tube plate, suitable for working conditions with a temperature difference of ≤ 50 ℃.
Floating head type: One end of the head can float, suitable for situations with a temperature difference of 100-150 ℃ (such as steam condensation).
U-shaped tube type: The heat exchange tube is bent into a U-shape, allowing for axial thermal expansion and suitable for extreme working conditions with a temperature difference greater than 150 ℃.
Flow diversion design: Flow deflectors (such as bow shaped baffles) are installed inside the head to evenly distribute the fluid to each heat exchange tube and avoid flow deviation.
Baffle plate (shell side fluid reinforcement component)
Function:
Change the flow direction of the shell side fluid to form multiple turbulent flows across the tube bundle (Reynolds number Re>10 ?).
Support the tube bundle to prevent vibration (anti vibration bars need to be added when the critical flow velocity is less than 3m/s).
Type and Parameters:
Single bow: The gap height is 20% -25% of the shell diameter, suitable for cleaning media.
Double bow: symmetrically arranged with notches, reducing pressure drop by 30%, suitable for high viscosity fluids.
Spiral baffle: continuous spiral channel, shell side heat transfer coefficient increased by 15% -20%, but manufacturing cost increased by 40%.
3、 Sealing and support system: ensuring long-term stable operation
Sealing structure
Tube side sealing: Heat exchange tubes and tube sheets are sealed by mechanical expansion (pressure ≤ 10MPa) or hydraulic expansion (pressure ≤ 30MPa).
Shell side seal:
Fixed tube plate: The shell is welded to the tube plate without dynamic sealing.
Floating head type: using packing seal (graphite packing) or mechanical seal (temperature resistant to 350 ℃), leakage rate ≤ 10 ?? Pa · m ³/s.
U-shaped tube type: The tube plate and shell are sealed with gaskets (commonly metal wrapped gaskets), with a temperature resistance range of -200 ℃ to 800 ℃.
Supporting and anti vibration components
Pull rod and distance tube:
Rod: Round steel with a diameter of 10-20mm, connecting the baffle plate and the tube plate, capable of withstanding fluid impact force (tensile strength ≥ 400MPa).
Distance tube: Length error ≤ ± 0.5mm, ensuring consistent spacing between baffles and maintaining fluid turbulence.
Anti vibration design:
Misalignment of baffle notches: Adjacent baffle notches rotate 90 °, disrupting fluid resonance frequency.
Damper: Install rubber damping blocks at the free end of the tube bundle to reduce vibration amplitude (≤ 0.1mm).
4、 Structural optimization direction (engineering application case)
Compact design:
Double shell structure: The shell is divided into two stages by longitudinal partitions, increasing the heat transfer area by 30% and suitable for large temperature difference conditions (such as atmospheric and vacuum distillation units in refineries).
Microchannel heat exchange tube: with a diameter of ≤ 3mm and a heat transfer area of 2500m ²/m ³ per unit volume, it is used for heat dissipation in electronic devices.
Anti dirt design:
Online cleaning: Install a rotating nozzle (pressure 0.5-1.0MPa) on the shell side and regularly flush the scaling layer (such as seawater desalination pretreatment).
Self cleaning coating: Nano hydrophobic coating (contact angle>150 °) is applied inside the tube, reducing dirt deposition by 60%.
Material upgrade:
High temperature resistant alloy: Inconel 625 (temperature resistance of 1000 ℃) is used instead of 304 stainless steel in gas turbine intercoolers.
Graphite heat exchange tube: corrosion-resistant and high thermal conductivity (120W/(m · K)), used in strong acid and alkali media (such as chlor alkali industry).